The future of high-performance heat exchangers starts with Mezzo Microtubes.
Learn how and why microtubes make a difference.
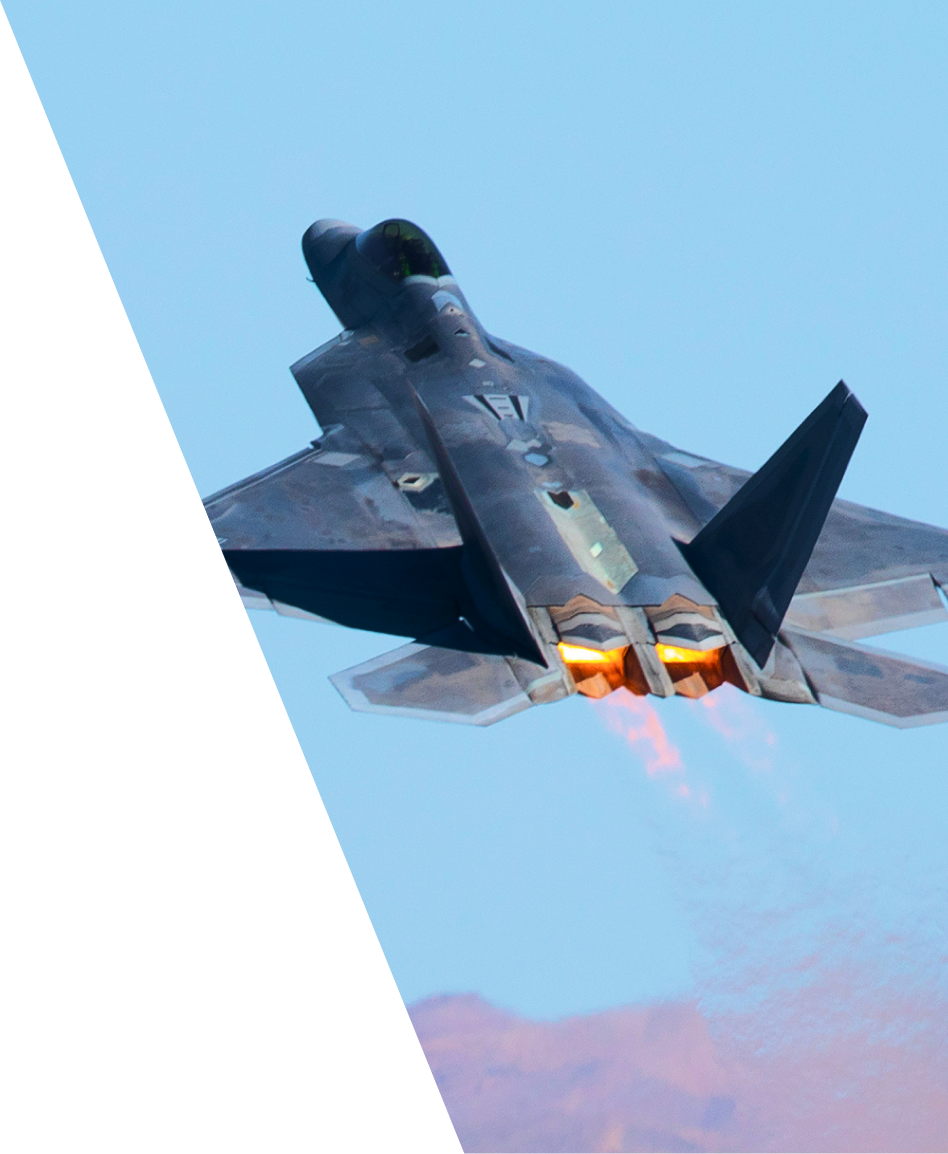
Microtube heat exchangers are:
- Compact & Lightweight
- Resistant to Air-Side Fouling
-
Optimal in High Pressure &
High Thermal Applications - Aerodynamic
- Reliable & Durable
- Corrosion Resistant
Microtubes provide extremely high performance across a wide array of applications. The ultimate reason for selecting microtubes varies by application, but in all cases, Mezzo provides its customers with industry-leading performance.
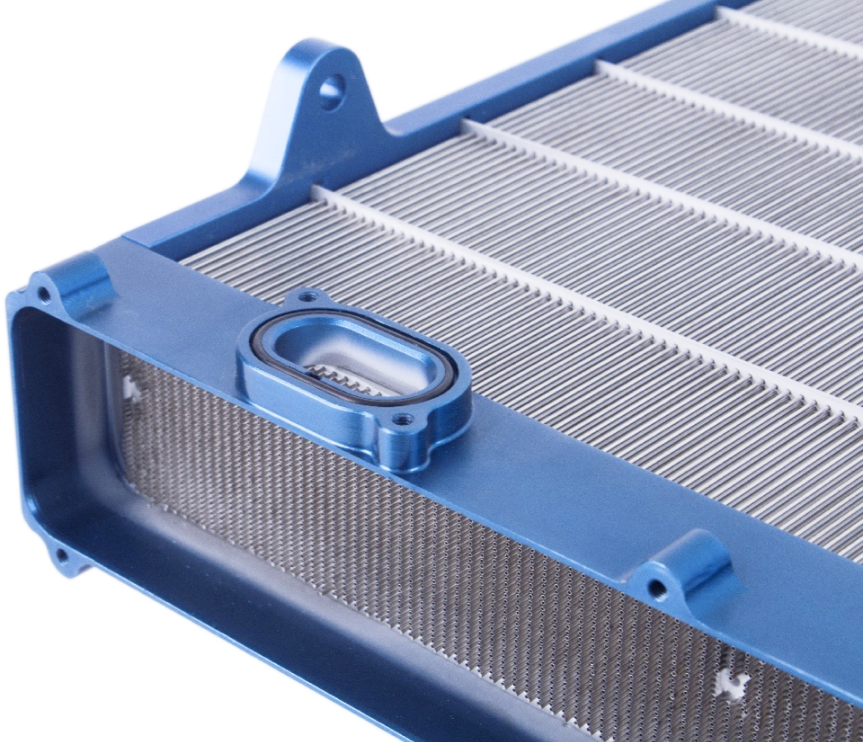
What is Mezzo Microtube Technology?
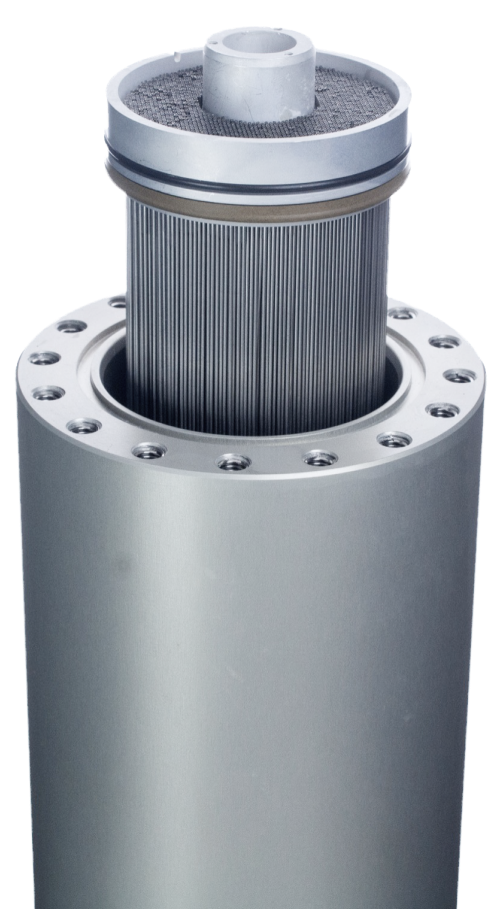
Mezzo Microtube: A tube with a diameter ranging from 0.2 to 3.0 mm. Most products fall between 0.5 and 2.0 mm in diameter.
Material: Various stainless steels, superalloys, titanium, and polymers.
A microtube heat exchanger core typically comprises of two tube sheets, which are planar and parallel to each other, and are connected by hundreds to tens of thousands of microtubes. These microtubes allow for the flow of one fluid inside them, while the other fluid flows over the outside of the tubes.
To support the tubes and guide shell-side flow through the core, additional components like header tanks, shells, midplates, baffles, and side plates are used.
Joining the tubes to the tube sheets is achieved by using various proprietary methods.
Several architectures are available for microtube heat exchangers, including multiple pass crossflow shell side, multiple pass crossflow tube side, cylindrical or rectangular cores, and pure counterflow (for cases where extremely high effectiveness is needed), among others. Unlike other heat exchangers that rely on fins to transfer heat, microtube heat exchangers are sometimes called “primary surface” heat exchangers, as they do not use fins to transfer heat from one fluid to the other.
Why Use
Mezzo Microtube Technology?
Simple scaling laws show that microtubes provide significantly more UA/volume (KW/K-m3) than heat exchangers that utilize larger diameter tubes or larger characteristic channel dimensions. The UA/volume scales with tube diameter approximately as 1/D2. So, a heat exchanger with 1.0 mm diameter microtubes will have a UA/volume ratio about 100 times greater than a heat exchanger with 10 mm diameter conventional-scale tubes.
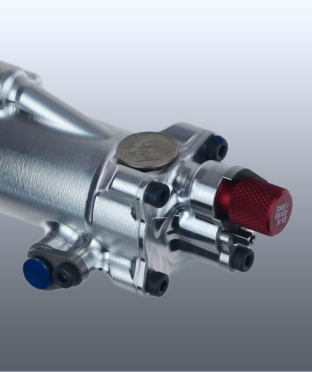
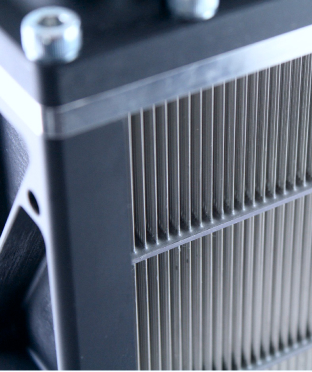
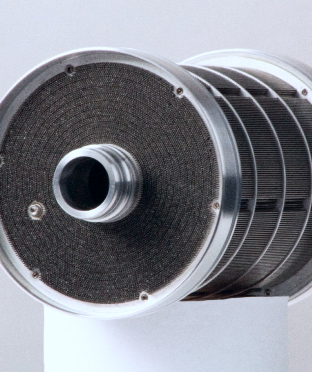
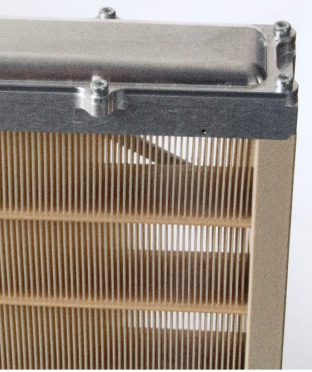
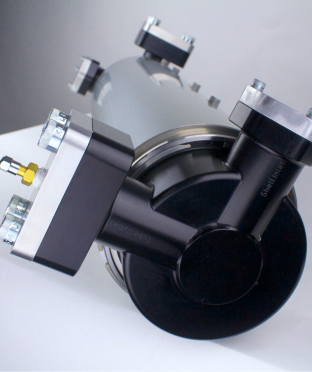
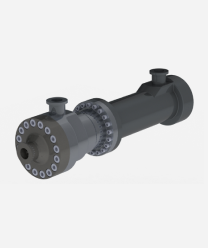
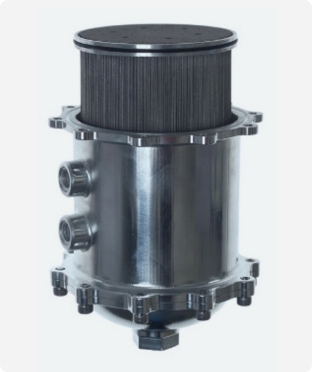